Kaikaku is een manier om in korte tijd een doorbraak te realiseren in een productiesysteem. In dit artikel wordt een Kaikaku beschreven bij een fabriek waar producten maar mondjesmaat op tijd werden geleverd. Met een Kaikaku, ook wel Kaizen blitz genoemd, is de gehele fabriek schoongeveegd en opnieuw ingericht.
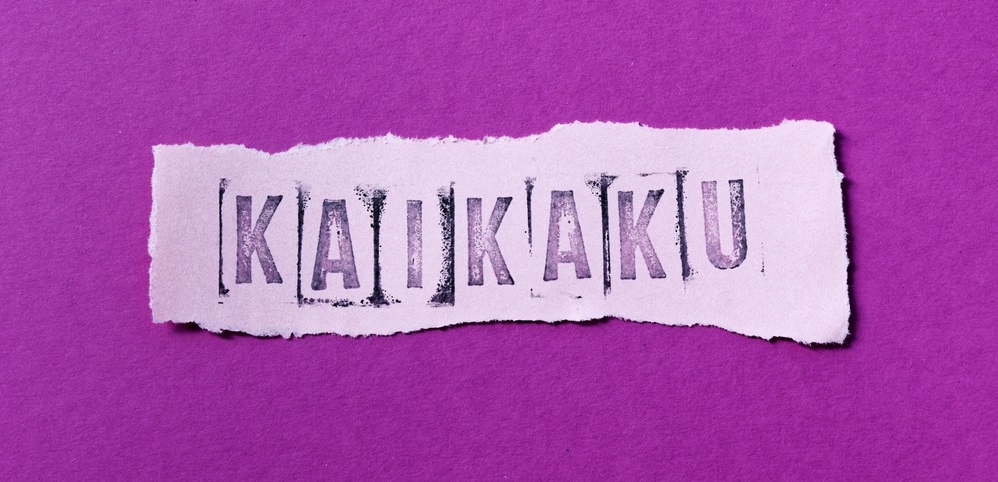
De Kaikaku werd toegepast op een afdeling van een assemblagefabriek voor metalen onderdelen. De afdeling lag vol met materiaal dat pas dagen later werd gebruikt. Iedereen was op verschillende plekken druk bezig om de producten in elkaar te zetten of was op zoek naar materiaal of gereedschap. Van enige flow was geen sprake, wel van veel werkkapitaal en work in progress (WIP) – en van onvoorspelbare levering van de producten.
Kaikaku voorbereiden
Er werd besloten een Kaikaku uit te voeren. Dit vraagt de nodige organisatie vooraf. Gedurende een Kaikaku wordt de productie enkele dagen volledig stilgelegd. Het is een snelle en ingrijpende wijziging van de productie lay-out. Via een DMAIC-werkwijze (Kaizen Blitz is de I van DMAIC) worden vooraf een aantal zaken geregeld zoals:
- omschrijving van de producten en de productenmix;
- inventarisatie van de processtappen;
- product-proces flowmatrix;
- maken van een plattegrond;
- doelen bepalen (ruimtebesparing, doorlooptijdreductie, WIP-reductie);
- inventarisatie belanghebbenden;
- planningsmogelijkheden (een week uitplannen bijvoorbeeld).
In de eerste fase worden de medewerkers actief betrokken om na te denken over de nieuwe lay-out, de inrichting van de werkplekken, de toestand van de gereedschappen en machines en de gewenste materiaalstroom. Er worden flip-overvellen opgehangen in de productiehal waar iedereen zijn ideeën kwijt kan. Daar wordt veel gebruik van gemaakt en er staan vaak waardevolle opmerkingen op.
Meten is weten
Vooraf worden veel metingen uitgevoerd, zoals de bewerkingstijden per werkplek, waarbij de verschillende productsoorten zijn onderscheiden. De totale doorlooptijd wordt gemeten en er is een spaghettidiagram gemaakt van de looproute van een medewerker die een product compleet maakt. In deze casus lijkt dat daadwerkelijk op een bord spaghetti. Er wordt heel veel heen en weer gelopen. Er zit duidelijk geen flow in de beweging van het product door de fabriek.
De metingen per werkplek leveren interessante informatie op.
De metingen per werkplek leveren interessante informatie op. Ten eerste blijkt dat de bewerkingstijden van de verschillende producten niet zo heel veel verschillen Ook blijkt er één bewerking tussen te zitten die gemiddeld drie keer zo lang duurt als de andere bewerkingen. Deze bewerking wordt dus in drievoud in de lijn opgenomen.
Dagindeling
De indeling van de dagen is standaard. We starten iedere dag om 6:00 uur met een kort koffiemoment om iedereen scherp te krijgen voor de opdracht van de dag. Om 11:45, vlak voor de lunch, is er ook een korte teambijeenkomst om te kijken hoe de dag vordert en of er nog zaken geregeld moeten worden voor de rest van de dag. Als bijvoorbeeld blijkt dat we achterlopen, kunnen er nog maatregelen genomen worden. De dag sluiten we gezamenlijk om 14:45 af met een korte terugblik en een lijst met nog open punten. Dat houden we vier dagen zo vol, alhoewel de laatste bijeenkomst op de laatste dag een wat ander karakter zal hebben.
Eenpuntslessen
De eerste dag wordt zoals afgesproken om 6 uur ’s ochtends gestart met een bijeenkomst. Daar bespreken we de uitgangspunten, bekijken we nogmaals wat we bedacht hebben en bespreken we de planning. Er is extra uitleg over de werkwijze en over een aantal methoden die we de komende dagen gaan toepassen, zoals de werkplekinrichting met de gereedschaps- en informatieborden, de plek voor de daily stand-up met het planningsbord en het opzetten van éénpuntslessen voor het vastleggen van de standaard werkwijze. Deze éénpuntslessen komen ook op de werkplek te hangen en worden zo snel mogelijk na afloop van de Kaikaku geschreven. Als er nog onderwerpen worden bedacht, kan dat op de centrale flip-over geschreven worden.
Met behulp van éénpuntslessen wordt de standaard werkwijze vastgelegd.
Kaikaku: ook opruimen en poetsen
Na de introductie wordt de hele hal leeggehaald. Dat maakt het mogelijk om de machines in de hal langs de kanten te zetten waar ze kunnen worden nagekeken en schoongemaakt. Voor deze dagen is extra technisch personeel ingeschakeld om alle machines goed na te kijken. De productiemedewerkers en de leiding nemen de poetsdoeken ter hand om de machines op te poetsen.
Er blijken nogal wat overbodige spullen te liggen waar jarenlang niet naar omgekeken is.
Alle materialen die op de werkvloer liggen worden ook weggereden naar vooraf vastgestelde plekken. Er lag veel materiaal, dus nam dat nogal wat tijd in beslag. De stellingen die in de ruimte staan worden ook allemaal leeggehaald, schoongemaakt en verplaatst, of afgebroken als ze niet meer nodig zijn. Er blijken nogal wat overbodige spullen te liggen waar jarenlang niet naar omgekeken is. Gelukkig zijn er voldoende containers besteld om het allemaal af te voeren.
Opnieuw inrichten
De laatste stelling is de tweede dag om half twaalf leeg. Nu is de hal echt leeg en kan de schoonmaak beginnen. Ook de wanden worden opgeknapt. Daarna kan het inruimen beginnen. Met de plattegrond in de hand worden de eerste machines op de voorgestelde plek gezet. Met tape bakenen we de werkplekken af en zetten we de eerste gereedschapsborden neer. Deze worden ook ingeruimd met het gereedschap dat we vooraf hadden verzameld. De volledig ingerichte borden worden gefotografeerd om als standaard te dienen.
Een aantal medewerkers begint al met het opschrijven van de standaardwerkwijze in de vorm van een concept-éénpuntsles. Deze moeten tenslotte bij de werkplekken komen te hangen en het doel is om er ook een aantal te hebben als de lijn aan het eind van de vierde dag wordt opgeleverd.
Het aansluiten van de machines gebeurt via een tijdelijke aansluiting maar zeker niet onveilig, de arbocoördinator zit daar bovenop met zijn beoordeling. De uiteindelijke aansluiting wordt gepland na afloop van de sessie, het is nu zaak om te zorgen dat de productie de vierde dag kan draaien zonder concessies te doen aan de veiligheid.
We brengen alleen de afgesproken benodigde materialen in de flow terug. Er is een kanban-systeem ontwikkeld waarvoor ook nieuwe stellingen zijn besteld. De verpakkingseenheden voor de spullen in het kanbansysteem passen goed, maar moeten ook opnieuw worden ingeruimd. Dat geldt natuurlijk ook voor de stellingen. Vooraf was het verbruik gemeten, dus we weten hoe de indeling van de stellingen moet worden.
Ook de informatieborden worden ingericht. De indeling die was bedacht wordt eerst met stift aangebracht. Als het goed blijkt te werken, zal er over drie weken een sticker gemaakt worden ter grootte van het whiteboard. Dan is het allemaal permanent.
De flow is terug met kaikaku
Langzaamaan vult de hele afdeling zich opnieuw met machines, gereedschapsborden, afgebakende werkplekken, materiaal en informatieborden. Aan het einde van de derde dag is alles al vrijwel klaar en is duidelijk zichtbaar hoe de flow moet gaan lopen. Je kunt nu gewoon aan het begin beginnen en de afdeling doorlopen en zien hoe het proces moet gaan.
De laatste dag zijn er nog wat zaken te regelen. Er ontbreken nog gereedschappen die aangevuld kunnen worden en ook in het kanbansysteem blijken niet alle producten aanwezig te zijn. Gelukkig zijn die producten niet nodig voor de eerste productierun.
Halverwege de vierde dag worden de productie en de grote klok gestart. In het begin van het traject is voorspeld wat de doorlooptijd zal zijn als de flow opnieuw zou worden ingericht. En het blijkt te kloppen. De flow loopt, de hoeveelheid materiaal in de afdeling is drastisch afgenomen, er is veel meer rust, de doorlooptijd is gereduceerd en de medewerkers hoeven niet meer zoveel te lopen.
Tevreden sluiten we op de vierde dag met een groepsfoto het traject af. Wat nog rest is een actiepuntenlijst om in de komende 30 dagen op te lossen, maar dat gaat goed komen.