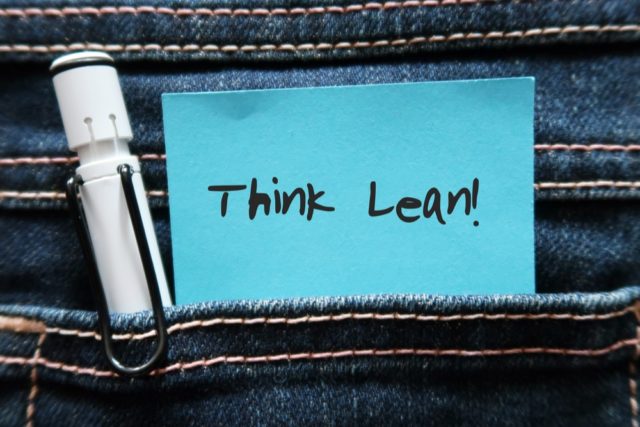
Lean leiderschap is gebaseerd op het principe van volhardendheid ((nebari tsuyosa)). Een Lean leider laat zich niet zo snel bij tegenslagen uit het veld slaan. Het doorvoeren van Lean betekent immers voor velen een nieuwe manier van werken en ander gedrag. Diverse barrières moeten worden overwonnen om in een situatie te geraken waarbij de hele organisatie continu streeft naar perfectie.
Sterker nog, bij het invoeren van Lean gaat wel eens iets mis, verloopt iets niet volgens plan of vallen de verbeteringen tegen. Het management moet dan niet te snel opgeven of juist medewerkers onder druk zetten, maar het moet de organisatie op sleeptouw nemen, stabiliteit en vertrouwen geven en een oplossingsrichting bieden. Deze volhardendheid – of het rotsvast vertrouwen in een goed resultaat (zonder de harde werkelijkheid, uit het oog te verliezen) – is eerder beschreven door Jim Collins (2001) als een belangrijk kenmerk van de high-performance-organisatie.
Verwachting versus gerealiseerde prestatie
Het invoeren van Lean is in de regel erg tijdrovend. Het vergt extra capaciteit en managementaandacht om ‘continu verbeteren’ in het DNA van de organisatie te krijgen, zodat iedereen streeft naar perfectie en voortdurendzoekt naar verspillingen om deze te kunnen elimineren. Dat is voor de meeste organisaties geen vanzelfsprekendheid.Het invoeren van Leanis ook omgeven met onzekerheid, juist omdat het voor veel organisaties nieuw is (en de invoering daarvan een paradigmaverandering vereist). Desondanks zijn bij de start van Lean de verwachtingen hoog. Vanwege de vele succesverhalen in de media kan het dan voorkomen dat de verwachte besparingen al ingeboekt worden voordat ze gerealiseerd zijn. En door de eenvoud van de Lean-verbeterinstrumenten komt het nogal eens voor dat organisaties een projectorganisatie met Lean-experts optuigen om Lean te kunnen invoeren, maar waarbij men van operationeel leidinggevenden en andere medewerkers verwacht dat ze daar tijd voor vrijmaken en tegelijk hun volledige dagtaak ernaast blijven doen. De kans op langetermijnsucces is dan niet erg groot.
Dit wreekt zich zodra de invoering van Lean wordt vertraagd, vooral als dan ook nog eens blijkt dat de operationele en/of financiële prestatie van de organisatie juist minder wordt, terwijl gerekend werd op forse verbeteringen.
invoeren van Lean.
Het is niet ongewoon dat de operationele prestatie iets stijgt na de aankondiging om met Lean te starten, vanwege de aandacht die er dan is voor de operatie; zie figuur 2-10. Deze stijging wordt echter snel weer tenietgedaan als de aandacht tijdelijk blijkt te zijn, of als er door onzekerheid in de organisatie angst ontstaat aangaande de nieuwe processen, nieuwe taken en nieuwe functies. De prestatie komt verder onder druk te staan als de organisatie ‘op spanning wordt gezet’ door druk van bovenaf en door het binnenhalen van (extra) externe Lean-experts, vaak met een eenzijdige focus op projectresultaat.
De druk is vooral groot als de dubbelzinnige situatie ontstaat waarbij de ‘ondersteunende’ stafafdeling of projectorganisatie zich uitsluitend richt op het invoeren van de geplande verandering, terwijl de lijnorganisatie zich vooral bezighoudt met de dagelijkse operatie (die bij de start van een Lean-traject vaak niet goed onder controle is). Dan is er het gevaar dat vanwege de tegenvallende resultaten de invoering van Lean nog meer onder druk komt te staan en dat het programma nog meer aandacht en tijd krijgt ten koste van het dagelijkse werk, waardoor de kans toeneemt op een verder inzakken van de operationele prestaties. Als dan vervolgens groepen medewerkers en teamleiders afhaken bij de invoering van Lean, dreigt er het gevaar van blijvende schade. Alleen door volharding van het management en door extra investeringen kan deze negatieve situatie worden omgebogen.
Lean doe je er niet even bij
Lean is niet iets wat u er even bij doet. Lean kan niet even worden ingevoerd door medewerkers (naast hun reguliere werkzaamheden) door rigoureus de voorraden of andere verspillingen te reduceren. Integendeel,
het invoeren van Lean vergt een behoorlijke investering in tijd, capaciteiten geld. Dat werd ook vroegtijdig onderkend door Toyota. Zo werden er binnen Toyota speciale dienstroosters opgesteld met ruimte voor het creëren van een cultuur van continu verbeteren. Bij de invoering van Lean werd er voor allerlei verstoringen en variaties gebufferd met capaciteit door het aanhouden van een tweeploegenrooster in een 8-4-8-4-schema (waarbij elke achtuursdienst gevolgd werd door vier uur stilstand voor eventuele uitloop, voor preventief onderhoud of het doorvoeren van verbeteringen) in tegenstelling tot de gebruikelijke drie- of vijfploegenschema’s; zie ook Schonberger (1982, p. 137).
Bron: Lean leiderschap
Door: Marcel van Assen