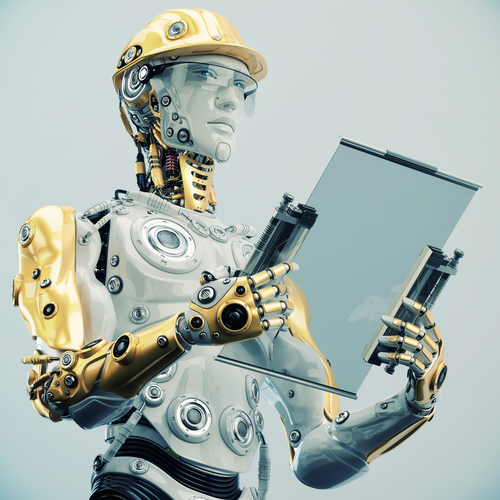
Airborne en Siemens bouwen op bedrijventerrein Ypenburg de eerste digitale fabriek in Nederland. Deze digitale fabriek doet tevens dienst als field lab, als ontwikkelcenter voor kennisinstellingen en bedrijven. Ontwerp, productieplanning, productie én kwaliteitscontrole worden in één virtuele omgeving ondergebracht. Met deze keuze voor flexible manufacturing bijten Airborne en Siemens in Nederland het spits af voor een revolutie in de maakindustrie, ook wel Smart Industry of Industrie 4.0 geheten.
De vergaande technologische ontwikkelingen zullen voor een omwenteling zorgen in de industriële sector. Met de digitalisering van productieprocessen bereidt het bedrijfsleven zich voor op een volgende stap in de industriële revolutie. De Duitsers noemen het Industrie 4.0, in de Verenigde Staten heet het Internet of Things en in andere landen, zoals Nederland, staat het bekend als Smart Industry of ‘slimme fabriek (de term ‘Smart Industry’ is bedacht door onderzoeksinstituut TNO en werkgeversorganisatie FME).
De slimme fabriek werkt zoveel mogelijk autonoom. Alle technologieën uit de informatie- en communicatietechnologie en de machinebouw worden gebundeld en geïntegreerd in materialen, onderdelen en machines waarvan ze deel uitmaken. Mede dankzij de beschikbaarheid van een grote diversiteit aan data kunnen binnen afzienbare tijd slimme robots realtime met elkaar communiceren en opdrachten uitwisselen gedurende het productieproces.
Field Lab
In Nederland is voor de digitalisering van de industrie in 2014 de Smart Industry Actieagenda gepresenteerd. Daarin staat wat er moet gebeuren om de kansen te verzilveren die de integratieproductie met informatietechnologie voor Nederland biedt. Kansen waardoor ondernemers sneller aan de slag kunnen met nieuwe businessproposities. Om hen daarin te ondersteunen met informatie en coaching zijn in 2015 door overheid, bedrijfsleven en kennisinstellingen zogeheten Smart Industry Field Labs startklaar gemaakt. Het gaat om enkele tientallen initiatieven voor praktijkomgevingen waarin ondernemingen uit diverse sectoren en kennisinstellingen doelgericht slimme industriële toepassingen ontwikkelen, testen en implementeren. Daarnaast zijn de Field Labs een podium voor onderzoeks- en onderwijsinstellingen op een specifiek thema in de Smart Industry. Zo’n thema is flexibele manufacturing, gericht op digitalisering en robotisering in de maakindustrie.
De eerste contouren daarvan zijn te zien in een vroegere productiehal van vliegtuigbouwer Fokker op voormalig vliegveld Ypenburg waar Airborne en Siemens de handen ineen geslagen hebben. Airborne is producent van composietonderdelen voor onder meer vliegtuigen en turbines; Siemens is automatiseerder van bedrijfsprocessen.
De hal is getransformeerd tot een spic en span werk- en demonstratieomgeving waar twee machtige robotarmen een centrale plaats innemen. Vrijwel geruisloos schuiven de robotarmen over een platform om er handelingen te verrichten aan een plaat van composiet, een supersterke kunststof, ook wel koolstofvezel of carbon geheten. De robots, afkomstig van de Duitse fabrikant KUKA, staan opgesteld achter een traliehek. Dat heeft een veiligheidsreden. ‘De robots kunnen razendsnel bewegen en wie er per ongeluk een klap van krijgt omdat hij te dicht in de buurt staat, overleeft het waarschijnlijk niet. Vandaar het hek’, zegt Frans van de Ven, directeur van Airborne, dat de hal samen met Siemens heeft gehuurd om er de eerste digitale fabriek van Nederland te ontwikkelen. Het is de taak van de robots om samen te werken bij de productie van onderdelen uit composiet die onder meer dienst doen in staartstukken van vliegtuigen of als rotorblad van turbines voor het opwekken van getijdenstroom (een soort windmolen onder water).
Innovatief produceren betaalbaar maken
De luchtvaart, met onder meer een klant als Airbus, de ruimtevaart en de maritieme industrie zijn de belangrijkste klanten van het twintig jaar oude Airborne (150 werknemers). Airborne is bij het vervaardigen van composietonderdelen nog grotendeels afhankelijk van handarbeid. ‘Dat handwerk hoort misschien thuis in lagelonenlanden als Mexico, maar zorgt bij ons voor hoge productiekosten’, zegt Van de Ven. ‘Dat is niet lang meer vol te houden in een concurrerende markt waar productkwaliteit en -veiligheid tot in de details zijn voorgeschreven en waar steeds hogere eisen gesteld worden. Failure is not an option. Streven naar affordability, naar ‘een betaalbare manier van innovatief produceren’ is volgens Van de Ven hét issue geworden in de nog traditioneel werkende tak van de maakindustrie waarin Airborne zijn geld moet verdienen.
‘We moeten met de productietijden en kosten van composieten als high-performance materiaal de komende vijf tot tien jaar grote stappen maken. Automatisering en krachten bundelen met een partij als Siemens zijn noodzakelijk om kosten te verlagen en de time-to-market te verminderen. Tegelijk willen we met deze digitale fabriek ook niet te veel een research&development-clubje worden. Hoofddoel is goede oplossingen voor de klant genereren. Er moet business gemaakt worden. Wel willen we andere bedrijven graag in meetings demonstreren wat er allemaal met digitale productie mogelijk is en fungeren we als experience center waar workshops en onderwijs door de TU Delft en Fontys Hogescholen gegeven worden.’
Dat juist Siemens vanuit de divisies Digital Factory en Process Industries&Drives veel inspanning steekt in de ontwikkeling van de digitale fabriek is niet zo verbazend. Het concern beschikt over alle software en – connected – hardwareoplossingen die nodig zijn voor zo’n slimme fabriek. ‘Wij willen bedrijven helpen’, zegt directeur Gert Bravenboer van de betreffende Siemens-divisie, ‘om flexibeler en concurrerender te worden. Er wordt wel veel gepraat over Smart Industry, maar de adoptiegraad is nog te laag. Om de BV Nederland een stevige push voorwaarts te geven, moeten we sneller, slimmer en beter gaan produceren. Dat is wat wij met deze de digital factory voor ogen hebben. Een zelfsturende plant waar de mens de opdrachten geeft, maar IT-systemen de informatie genereren op basis waarvan de productie geautomatiseerd plaatsvindt. En we hopen dat dit klanten uit alle industriesectoren zal inspireren.’
Snelkookpan van innovatie
Voordat Gert Bravenbroer van Siemens en Frans van de Ven van Airborne elkaar ontmoetten – want dat gebeurde pas toen ze naast elkaar in het vliegtuig naar de Hannover Messe zaten – had Bravenboer de olie- en gasindustrie als de ‘meest conventionele bedrijfstak’ ingeschat. ‘Met boorplatforms die 30, 40 jaar mee moeten. Dat de ruimtevaarten luchtvaart nog trager en behoudender bleken te zijn, wist ik niet. Frans van de Ven overtuigde mij dat het in zijn bedrijf helemaal anders moet omdat in zijn tak van sport de traditionele relatie leverancier-klant verandert en het kostenvraagstuk dominant wordt. Bij de opzet van zo’n nieuwe productieplant voor Airborne gaat het om een paradigmaverschuiving die leidt tot een disruptief businessmodel. Ofwel: een blanco A4 als begin, vergelijkbaar met een start-upbedrijf, voor een nieuwe wijze van produceren. Disruptief, omdat Airborne groot is geworden met het volledig met de hand maken van composietproducten, en dat in een omgeving die geen fouten accepteert en waar kwaliteitszorg topprioriteit heeft. Het leek ons al met al een fascinerende opgave te zien wat er zou gebeuren als we de volledige soft- en hardware voor digitale productie in één keer in de fabriek van Airborne zouden neerzetten. Dus zeiden we tegen elkaar: ‘We gaan het gewoon doen’, waarbij er dan wel een klantpropositie voorhanden moet zijn. Dan zet je er namelijk ook een deadline tegenaan en wordt het een snelkookpan van innovatie. De volledige keten van design, simulatie, planning en productie, testen en supply chain management wordt in één virtuele omgeving ondergebracht.’
Intelligente motion control
Niet de robots in de fabriek op Ypenburg zijn overigens uniek; uniek zijn de end-effectors, ofwel de ‘koppen’ op de robotarmen, met de intelligente motion control van Siemens. Bravenboer: ‘Deze robots zijn echte makers die een ambacht uitoefenen, die denken met hun kop. Dat is Formule 1 rijden in de wereld van composiet.’ Van de Ven: ‘De kop is, samen met de besturing, het kroonjuweel van het geautomatiseerd systeem, dat zelf bepaalt welke stappen daarvoor nodig zijn. Is de ene robot klaar met snijden met een lasermes of het opvullen van een tape in een mal, dan zal de andere vanzelf een andere taak overnemen, frezen of een gaatje boren bijvoorbeeld. De data die de koppen genereren zijn ook weer bruikbaar voor het finetunen van het ontwerp, het proces en het maken van nieuwe producten. De flexibiliteit van de robot zorgt ervoor dat je veel verschillende complexe producten in kleine series efficiënt kunt produceren. Dat levert bovendien veel digitale procesinformatie op waarvoor je bij handenarbeid een hele papierwinkel op orde moet brengen.’
Kenmerkend voor de maakindustrie is een keten van veel toeleveranciers.
Geen zorgen over kwaliteit
Essentieel is uiteraard om in de digitale fabriek de standaards voor kwaliteit te waarborgen. Daarover maakt Van de Ven zich geen enkele zorgen. Hij is er zelfs heilig van overtuigd dat de kwaliteit zal toenemen. ‘Op de kop van de robotarm komt een camera die meekijkt hoe de robotarm een laag composiet in een mal legt. Deze robot kan straks een aantal categorieën fouten onderscheiden om de kwaliteit van het legproces te waarborgen. Dat maakt de robot nog smarter. Gebeurt iets niet goed, bijvoorbeeld als de camera bubbeltjes in het carbon registreert, dan geeft de camera een signaal en passen we het proces aan. Nu moeten wij bij wijze van spreken alles onder een vergrootglas bekijken.’
Bravenboer: ‘Het baanbrekende aan het concept van de digitale fabriek is dat we één aorta voor datastromen gaan gebruiken. Iedereen die in de keten van Airborne een rol speelt, put er zijn informatie uit en stopt er ook weer nieuwe data in, waar men in andere stappen wat aan kan hebben. De ontwerper kan dan vaststellen waar het in het productieproces spaak loopt. Maar het systeem past ook automatisch voor de klant de documentatie aan als het ontwerp wijzigt. Data zo efficiënt mogelijk hergebruiken betekent dat je data die je eerst nodig had voor een staartstuk voor bijvoorbeeld een Boeing-vliegtuig, straks weer kunt aanwenden voor een nieuw type vliegtuig.’
Lego-bouwstenen
‘We reiken de klant als het ware een automatiseringsplanning aan’, zegt Van de Ven. ‘Kenmerkend voor de maakindustrie is een keten van veel toeleveranciers. De ene levert aan de andere, totdat het uiteindelijk de eindklant bereikt. Wat we nu doen is een aantal bouwstenen voor zo’n automatiseringsoplossing inregelen en robuust maken, de fase van start-up naar scale-up. Deze zogenoemde block chain technologies kun je vergelijken met een Legodoos met bouwstenen, ofwel modules die we inzetten om een volledige automatiseringsoplossing voor de klant te kunnen maken. Een voorbeeld uit de ruimtevaart waar we aan werken heeft te maken met de armen van satellieten die voor de energievoorziening van de satelliet zorgen en voorzien zijn van zonnecellen. Deze cellen zitten straks bevestigd op platen van carbon die Airborne in geautomatiseerde productie zal aanbieden aan een joint-venture van Airbus en Branson. Het gaat om 900 satellieten die in 2017 om de aarde worden gebracht en overal ter wereld het internet toegankelijk zullen maken.
Van de Ven: ‘Wij kunnen met onze digitale fabriek deze platen voor de zonnecellen leveren voor 30 procent van de kostprijs van handmatige productie. Dankzij onder meer een intelligenter maakproces halen we dus 70 procent van de kosten uit de keten. Alle bouwstenen hiervoor zijn inmiddels aanwezig.’
Smart Industry is ook een aanjager van sociale innovatie, van duurzame inzetbaarheid van mensen.
Voor het Franse industriële concern Alstom, actief in de energiesector, maakt Airborne composietbladen voor getijdenstroomturbines die onder water energie opwekken. Van de Ven: ‘Het gaat op jaarbasis om minimaal 300 bladen, van 16 meter of langer. Daarvoor gebruiken we composiet als materiaal. Deze bladen hebben onder water enorme krachten te verduren. In onze digitale fabriek gaan we dat fabricageproces uitontwikkelen. Daarna gaan we met die kennis de fabriek van Alstom in Normandië bouwen die deze bladen kan produceren. Als Airborne verkoop je dus straks geen producten meer maar productielijnen. Wij weten bijvoorbeeld nu al hoe we de turbinebladen smarter, ofwel hydro-elastisch kunnen maken zodat ze nog meer van deze krachten gebruikmaken en meer energie opwekken. We weten ook dat we in deze bladen sensoren kunnen aanbrengen, die als informatiedrager fungeren. Alstom is nog niet overstag voor deze vernieuwingen, maar ondertussen gaan we door om deze innovaties al in het toekomstig design aan te brengen. En kunnen we straks in één keer de sprong maken als de klant erom vraagt.’
‘Aan een Deense klant, het bedrijf Terma, een aerospace manufacturer, gaan we dit najaar leveren, waardoor routinematig handwerk dat geen waarde toevoegt overbodig wordt, zoals bij vier medewerkers die nu niets anders doen dan lapjes carbon sorteren en op de juiste plek leggen. Door dit werk te automatiseren, en dat geldt voor veel arbeid dat door robots overgenomen wordt, kunnen ondernemingen medewerkers inzetten op plekken in het proces die meer toegevoegde waarde opleveren. Robotisering zal veel laagwaardige functies vervangen door werk dat uitdagender, interessanter en minder monotoon is. Smart Industry is wat dat betreft ook een aanjager van sociale innovatie, van duurzame inzetbaarheid van mensen, vooral nu binnenkort een grote groep werknemers in de Nederlandse industrie met pensioen zal gaan en er tekorten dreigen. Daarom moet je nu investeren in het opleiden van mensen en ze leren om samen te werken met robots, iets wat vooral jongeren aanspreekt.’
Veel klantvragen
Sinds de opening van digital factory in december 2015 hebben Siemens en Airborne al ruim twintig vragen van klanten bereikt. Klanten die zoeken naar innovatieve en betaalbare productieoplossingen en hopen dat de digital factory hen de sleutel kan leveren. Bravenboer: ‘De interesse is boven verwachting groot. Er zijn al een kleine duizend mensen op bezoek geweest, van vertegenwoordigers uit healthcare, scheepsbouw tot vliegtuigindustrie. Deze fabriek trekt als een magneet. Maar we moeten prioriteiten stellen. Geld en mensen zijn niet oneindig beschikbaar. Veel van de dingen die we gaan doen, zoals het integreren van al die interfaces, zijn proof of concept. Het is nu nog te vroeg om te zeggen of daar ook een verdienmodel achter zit, of het rijp is voor de markt. Die voorbeelden moeten nog komen.’
Arbeid zit niet meer alleen in het fysiek maken van producten, maar in het bedenken, testen en simuleren van oplossingen voor slimme productiemethoden.
‘Mooi aan deze ontwikkeling op Ypenburg vind ik vooral dat de maakindustrie uit haar schulp kruipt en nieuwe zuurstof tot zich neemt. Doordat in netwerkverband wordt geïnnoveerd en we kennis via platforms uitwisselen, kan snel worden geschakeld. Daardoor zijn er ook explosies aan nieuwe toepassingen mogelijk.’
‘We hebben de factor arbeid in het verleden verplaatst naar lagelonenlanden. Maar arbeid zit ‘m tegenwoordig niet meer in het fysiek maken van producten, maar in het bedenken, testen en simuleren van oplossingen voor slimme en flexibele productiemethoden voor op maat gemaakte producten in kleine series, zoals Airborne dat doet. Productiemethoden die bovendien passen in het idee van de circulaire economie die op ons afkomt, met energiezuinige oplossingen en zo min mogelijk afval.’
Bron: Sigma 1, 2016