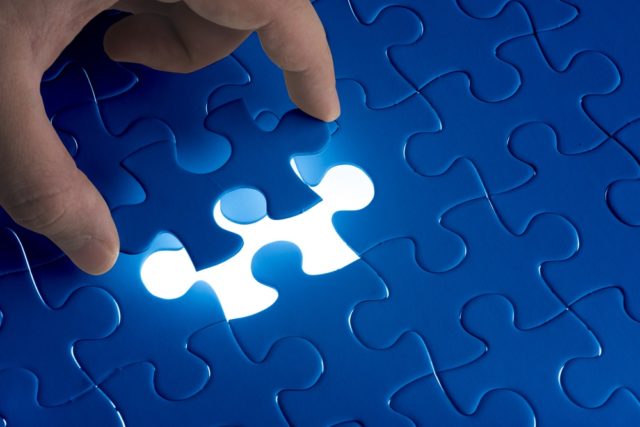
Voor complexere problemen is behalve een goede probleemformulering ook een gestructureerde probleemoplossingsaanpak nodig, met alle essentiële elementen van de wetenschappelijke methode: een iteratieve cyclus van hypotheses formuleren, hypotheses testen en volgende hypotheses ontwikkelen. Zoals bijvoorbeeld het A3-proces.
Een effectieve, eenvoudige aanpak is Toyota’s beroemde (lean) A3-aanpak. Die aanpak en dat formulier we hebben in dit artikel aangepast voor gebruik in niet-productieomgevingen. Het A3-formulier (zie kader) verdeelt het gestructureerde probleemoplossingsproces in vier hoofdstappen (de vier kwadranten). Elke hoofdstap heeft kleinere subfasen (onder de stippellijn).
Probleembeschrijving
In stap 1, het kwadrant linksboven, formuleer je een heldere probleembeschrijving. Onderin, bij Achtergrond, neem je voldoende informatie op om de probleembeschrijving duidelijk te koppelen aan de grotere missie en doelstellingen van de organisatie, en kun je het waarom van de probleemoplossingsinspanningen beschrijven.
Huidig design
Stap 2 in het A3-proces is het documenteren van het huidige procesdesign, door het werk direct te observeren. Door automatische verwerking en onbewuste routines, kunnen de meeste mensen niet precies beschrijven hoe ze hun werk uitvoeren. Managers moeten daarom zelf op de werkplek (in lean-taal: Gemba) gaan kijken, om te begrijpen hoe het dagelijkse werk nou echt wordt gedaan en welke (vaak eenvoudige) verbeteringsmogelijkheden er zijn.
Een team bijvoorbeeld, wilde de factuurverwerkingstijd terugdringen. Toen het proces werd doorgelicht, bleek dat elke factuur enkele dagen bleef liggen, omdat de juiste grootboekcode moest worden toegevoegd; terwijl die code voor dit type factuur altijd hetzelfde was! De doorlooptijd kon simpel worden verkort, door vooraf de code op het formulier te printen. Het werk nauwlettend observeren brengt vaak verschillende veronderstellingen naar boven.
Root Causes
Een volgende stap is het analyseren van Root causes en het expliciet koppelen van je waarnemingen aan de probleemformulering. Er zijn verschillende technieken voor root cause-analyse, zoals ‘vijf keer waarom’ waarbij de onderzoeker vijf keer de ‘waarom’- vraag stelt, in de hoop te komen tot de echte, fundamentele probleemoorzaak.
Doel van alle root cause-aanpakken is te begrijpen hoe het waargenomen probleem verankerd is in het bestaande design van het werksysteem, in plaats van meteen, via patroonmatching, voor de hand liggende oorzaken en oplossingen aan te wijzen. Customerserviceproblemen bijvoorbeeld, worden vaak toegeschreven aan dingen die ‘uitzonderlijk zijn en eenmalig gebeuren’. Dieper graven echter, kan dan uitwijzen dat processen om servicemedewerkers te trainen of klanten te instrueren tekortschieten. Een goede root cause-analyse koppelt data uit het onderzoek aan de probleembeschrijving en verklaart hoe het huidige systeem de problemen genereert, niet als uitzonderlijk geval, maar als onderdeel van routinematig gedrag.
Doeldesign
Nadat je kenmerken van het werksysteem hebt gelinkt aan het probleem dat je wilt oplossen, breng je bij Doeldesign een geüpdatet systeem in kaart, dat het probleem aanpakt en dat effectiever functioneert. De benodigde veranderingen zijn vaak eenvoudig, zoals ‘voortaan de grootboekcode printen op het formulier’ of iets gecompliceerder, bijvoorbeeld ‘aanpassing van trainingen’. Meestal gaat het om specifieke, gerichte aanpassingen die voortvloeien uit de root cause-analyse.
Probeer niet alles tegelijk op te lossen;stel het minimale aantal veranderingen voor dat je snel dichterbij je doel brengt. Vul nu het Verbeteringsdoel in. Een goede doelbeschrijving bouwt direct voort op de probleembeschrijving (‘24% van onze klantenservice interacties is niet-positief, terwijl onze target <5% is’) door te voorspellen hoeveel van de kloof je gaat dichten en in hoeveel tijd (‘negatieve klantenservice-interacties met 50% terugdringen in 60 dagen). Heldere doelen zijn heel motiverend en voorspellingen ondersteunen effectief leren. Bepaal ten slotte de Leiderschapsrichtlijnen: grenzen of beperkingen die niet overschreden mogen worden (zoals, ‘kosten beperken zonder kwaliteitsconcessies’).
Executieplan in het A3-proces
De volgende stap is het experiment houden. In dit kwadrant schets je een plan om het voorgestelde design te implementeren, onderverdeeld in duidelijke, afzonderlijke activiteiten (‘herdrukken factuurformulier’ of ‘dagelijkse meeting om kwaliteitsissues te bespreken). Ken aan elke activiteit een eigenaar en opleverdatum toe. Voer nu het plan uit en behaal je doel. Los het probleem niet alleen op, maar trek er ook lessen uit. Volg de activiteiten en laat eigenaren in tussentijdse projectrapportages aangeven of hun onderdeel voor- of achterloopt, welke lessen zijn geleerd en welke ondersteuning ze nodig hebben.
Onder Resultaten tracken meet je de voortgang richting het doel. Bij ‘negatieve interacties 50% terugdringen in 60 dagen’ kun je, bijvoorbeeld, tussentijdse (wekelijkse) doelen stellen, die je in de eerste kolom zet. Blijf ook meten ná het behalen van doelen: je wilt immers blijvende resultaten. Is het project voltooid, dan leg je helemaal
onderin de belangrijkste Lessen en nieuwe kansen vast. Als voorspellingen zijn overtroffen, wat zegt dat over toekomstige mogelijkheden? Het niet-behalen van doelen daarentegen, kan onderdelen van het werksysteem blootleggen die je minder goed begrijpt dan gedacht.
Tot slot, misschien wel het allerbelangrijkste: welk probleem ga je nu aanpakken? Een goed functionerend proces – in productie, klantenservice of waar ook – is het product van talloze kleine veranderingen en het oplossen van één echt probleem brengt vaak vele andere dringende problemen naar boven.
Bron: MIT Sloan Management Review
Door: Nelson Repenning, Don Kieffer en Todd Astor